At Living Edge, we believe the circular economy has the power to help tackle some of our industry’s biggest challenges. A circular business model relies on three areas of focus functioning together. In this series of short articles, we’ve been exploring these three topics, proposing the opportunities and challenges presented by each.
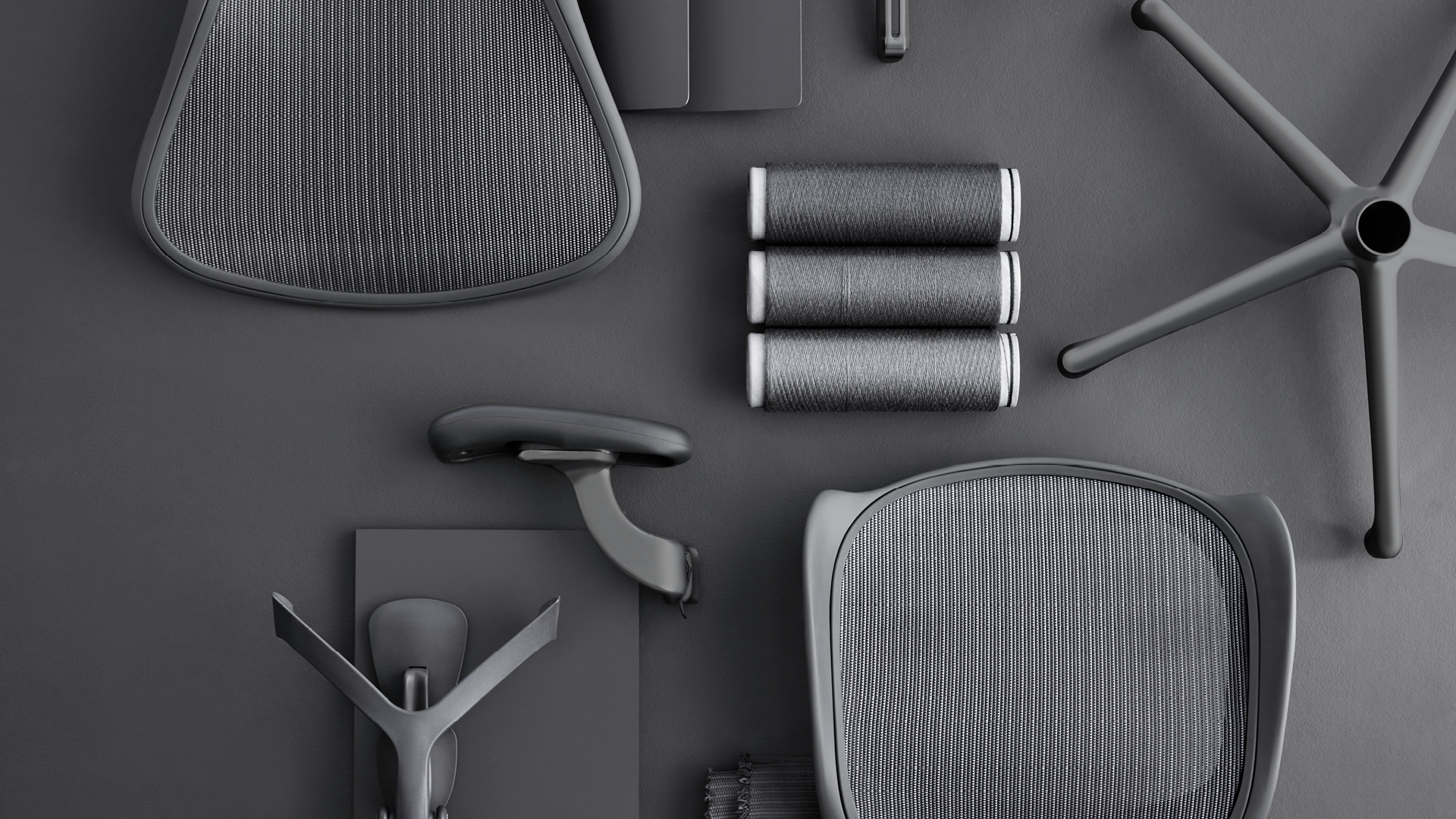
The Ellen MacArthur Foundation, a leading advocate for circularity, propose that the circular economy is based on three key principles, driven by design: eliminate waste and pollution, circulate products and materials at their highest value, and regenerate nature. It is hoped that by following these principles, we can decouple growth from the consumption of natural resources and create an economic system that supports and regenerates the natural and social capital society relies upon.
To successfully circulate furniture products, and the valuable materials used to make them, we need to find more effective ways to recover furniture from users when they reach the end of each use lifecycle. And once we have recovered those products, we need to provide end-of-life pathways that enable the repair, refurbishment, reuse, or resale of the product, or accessible solutions for disassembly and recycling. At Living Edge, we think of these end-of-life pathways as a hierarchy of circular outcomes. Our mission is to achieve the best possible outcome for every product we recover, prioritising repair, reuse, and resale, whilst expanding our recycling capability to prevent products and materials being lost to landfill.
br>
At Living Edge, we think of these end-of-life pathways as a hierarchy of circular outcomes. Our mission is to achieve the best possible outcome for every product we recover, prioritising repair, reuse, and resale, whilst expanding our recycling capability to prevent products and materials being lost to landfill.
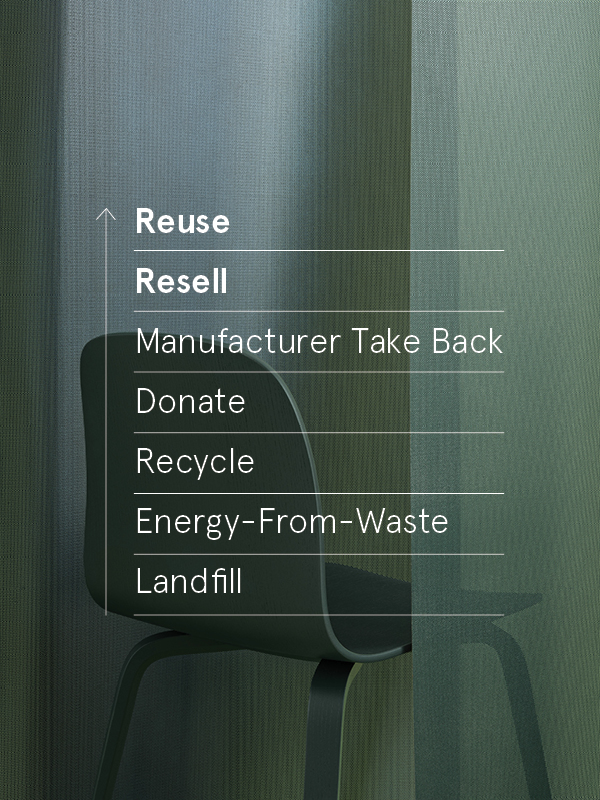
The need for these sustainable end-of-life pathways is particularly apparent in the commercial sector, where the pace of consumption and disposal is often driven by commercial property lease terms and organisational change. These drivers can create a disconnect between the potential lifespan of a product and the actual amount of time they are used for before they are retired from use. This is where a tension begins to appear – between the need for flexible approaches to property leasing to attract tenants and diversify and maximise building use, and the need to maximise the useful life of products. Arguably, this disconnect is one of the biggest causes of the 35,000 ton a year waste problem in the commercial furniture industry.
To overcome this challenge, we need to make it easier and more attractive to repair, refurbish, and reuse products, we need to create new markets to resell products, and we need to rethink our perception of the value of used products. This new way of thinking is reliant on design for disassembly, high-quality manufacturing, and sustainable materials that are durable enough to withstand multiple use lifecycles. Not only will this help tackle our industry’s waste issue, but it also provides an opportunity to reduce lifecycle embodied energy by leveraging the significantly lower emissions footprint of reused, and refurbished products. The circular economy is undoubtedly one of the biggest opportunities in the journey to net-zero.
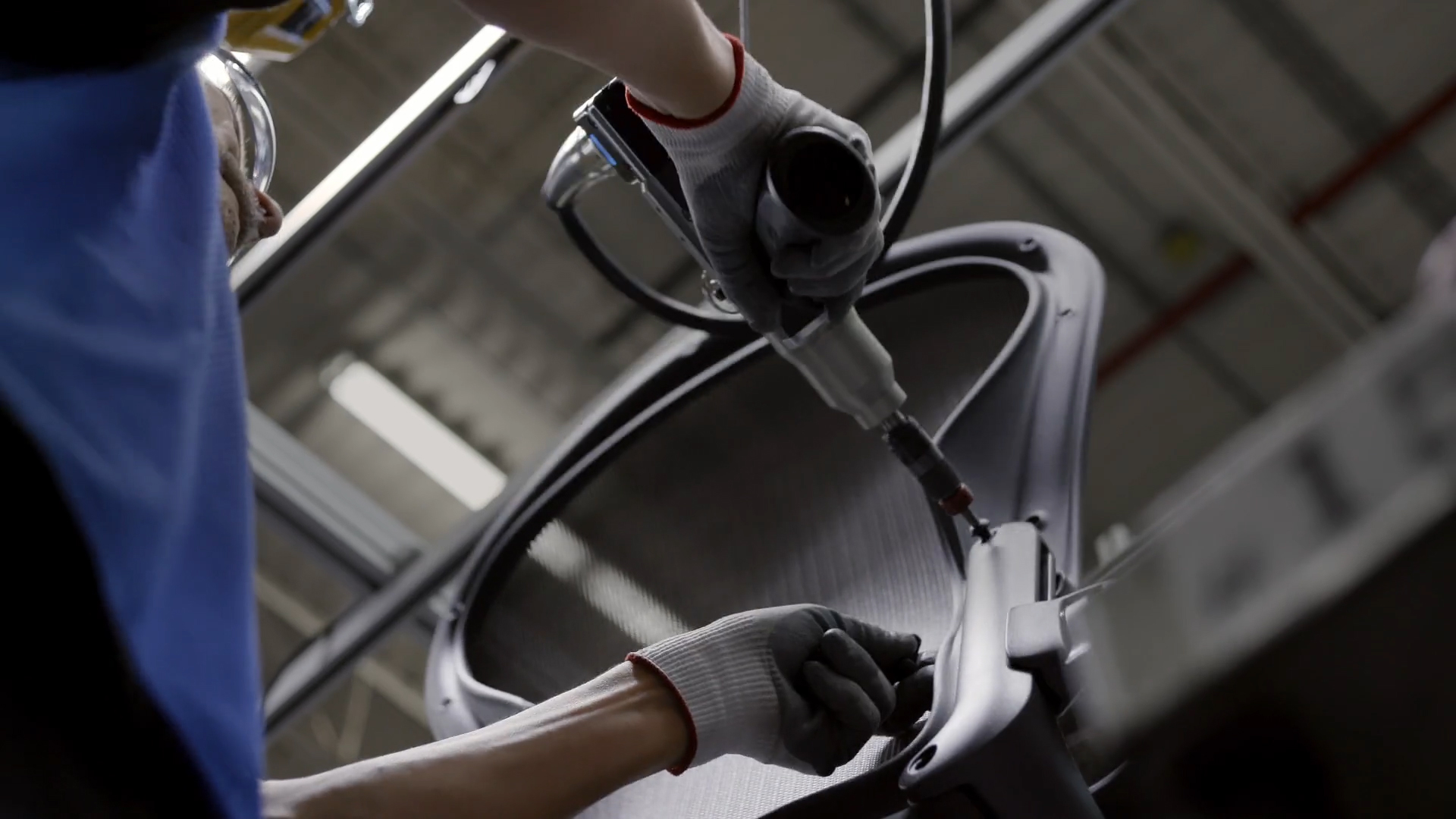
To respond to this opportunity, Living Edge has launched Relive, a sustainability program that aims to create a second life for Living Edge products. Relive achieves this aim by enabling the reuse and resale of Living Edge products through: • A repair & refurbishment service to help customers reuse their assets, and, • A sales platform for pre-owned Relive products.
A Relive product is a Living Edge product that has been recovered from the market through take-back and buy-back agreements and reconditioned for sale as a preowned product, backed by a Living Edge’s Relive warranty. The Relive program helps to deliver the top two outcomes in the circular hierarchy of end-of-life outcomes – reuse and resell.
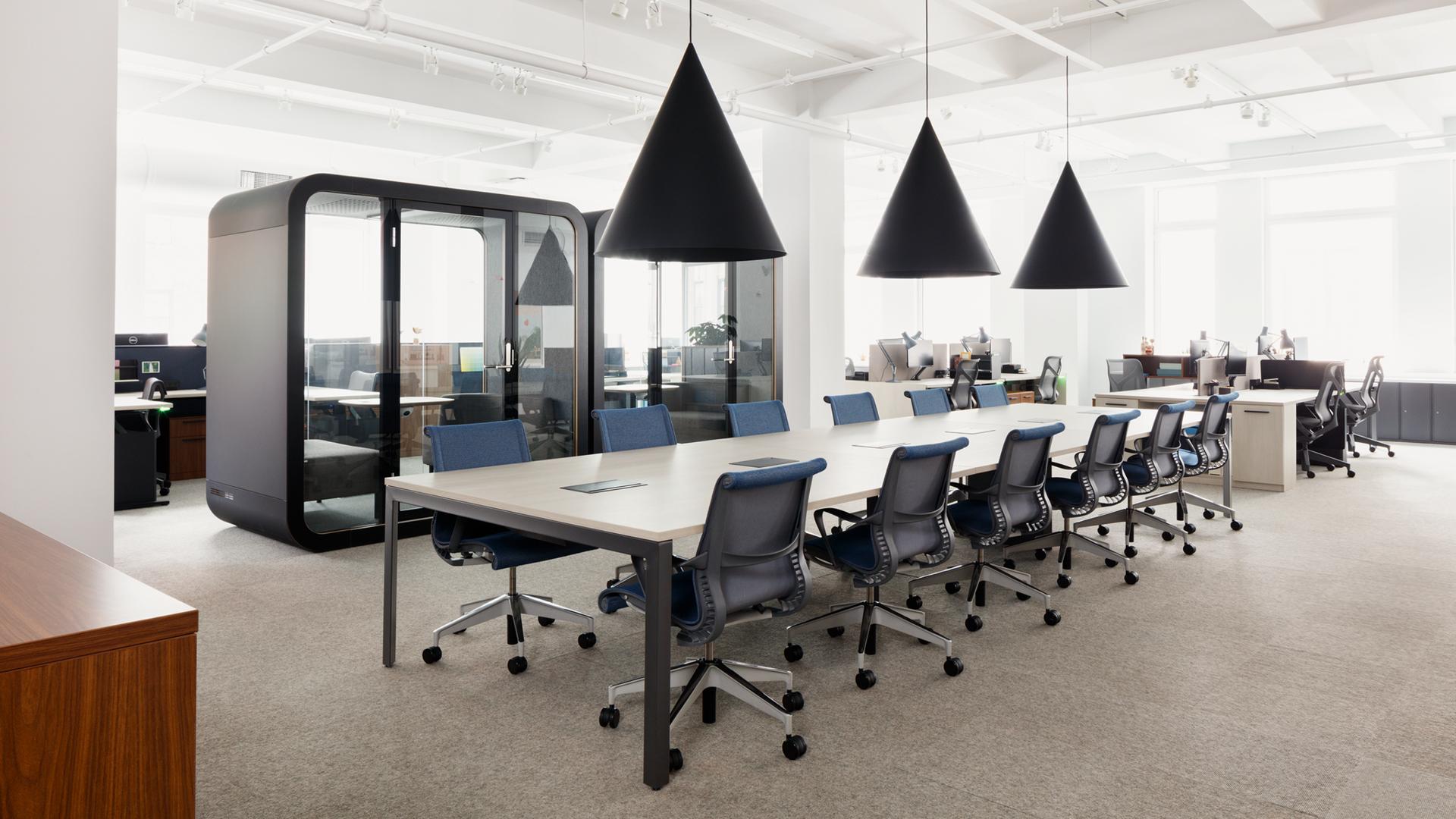
Living Edge already has a long history of delivering these services to its customers through its commitment to customer service and we estimate that since 2020, we have helped service and redeploy over 12,500 Herman Miller task chairs, diverting 234 tons of furniture from landfill.
We have already seen great success with the Relive program; our Melbourne team has recently helped a leading beauty and cosmetics group service and reupholster eighty 26-year-old Herman Miller Equa chairs for reuse at their stunning new Richmond office. The chairs were manufactured in 1996 and have already been through one significant refurbishment, making this their third lifecycle. We have also taken our first steps in refurbishing and reselling Relive products, with a major finance organisation purchasing preowned Eames Aluminium Group chairs and refurbished Herman Miller Setu chairs. We believe that Relive will allow us to take a more proactive approach to promoting and enabling circular end-of-life outcomes in the commercial furniture market.